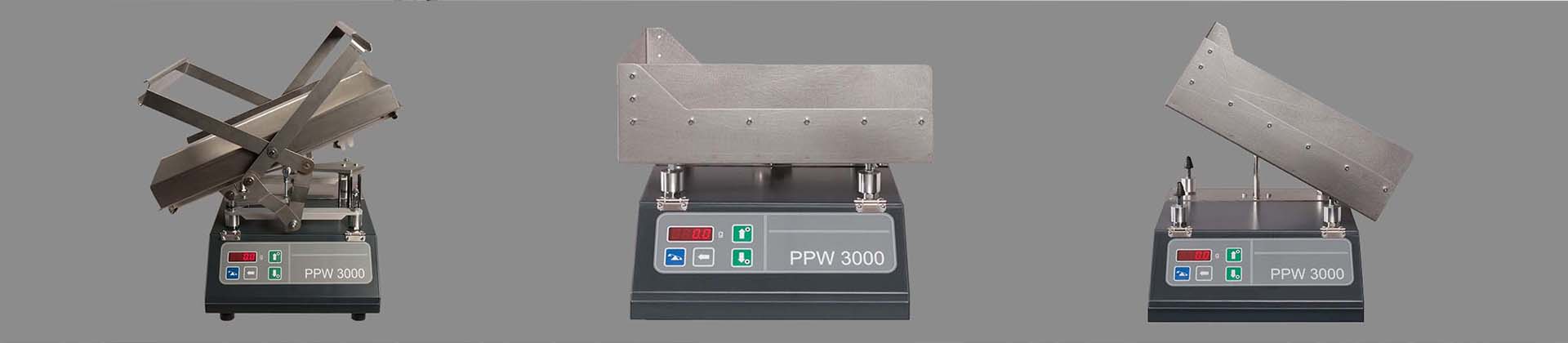
Pressure die-casting and injection moulding are continuous production processes. At some point hot-chamber and cold-chamber pressure casting machines produce hundreds of products with constant quality in pre-determined cycles.
Producing metal castings from rejects does not pose any problem, since defective castings can be in 100% used as secondary raw material. Damaged moulds and trimming tools, energy consumption, loss of quality and production downtime, however, can quickly reduce turnover or significantly increase the costs.
Therefore, continuous quality monitoring is also recommended for pressure die-casting. An weight sensing devices is one of the most important elements for ensuring mould quality and protection.
Optimal system control with precise measurement of cast mass
The easiest cast parameter to measure is its mass. As long as the clamping force and molten metal pressure are correct, and there are no changes in the mould cavity of a hot-chamber or cold-chamber pressure casting machine or an injection moulder, each cast should weigh the same.
What creates variable quality is the lower pressure which impairs cast density, that – in turn – reduces its weight. Similar adverse effects are brought by pressure spikes that occur during the casting process in the mould cavity. On the other hand damage to the mould or pressure changes in molten metal can cause an increase in the cast weight above the tolerance limits.
An weight sensing devices takes over a freshly cast element and weighs it. It owes its name to the fact that the cast falls out of the mould into the tray of the weight sensing devices. Weight is related to the control system of the pressure casting machine. When a mass deviation beyond the strictly determined tolerance is detected in the cast, the weight sensing devices stops the production process and trips an alarm.
Design and operating principle
The weight sensing devices is made of a tray, turning gear and a weighing module. The latter is interfaced with the control system of the pressure casting machine. Modern weight sensing devices have a pneumatic turning gear which, together with the electronic weight control, can reduce cycle time. A solid load cell is designed to receive falling casts, including heavy ones. An weight sensing devices is not permanently fixed to the pressure casting machine, but is simply placed further down the line under the chute, next to the pressure casting machine, and electronically connected to the production line.
Top-class weight sensing devices by Fiss
Despite having simple design, the weight sensing devices are effective units that help to ensure the quality of pressure die-casting and injection moulding. Both their mechanical design and measuring electronics must operate flawlessly for a long time. Specialist knowledge is required to manufacture, maintain and service these units.
Our weight sensing devices have standard interfaces and can be connected to all common pressure casting machines and injection moulders.
Our weight sensing devices can be used in
hot-chamber or cold-chamber pressure casting machines of the following brands:
- Frech
- Colosio
- Agrati
- IDRA
- Italpresse
- URPE
- LK-Machinery
- YIZUMI
- Techmire
- Bühler
- Weingarten
injection moulders of the following brands:
- Arburg
- Dr. Boy
- Battenfeld
- Krauss Maffei
- Demag
- Netstal
- Geiger
- Ferromatik Milacron
- Engel
We repair weight sensing devices fast and for a good price. Well maintained and regularly serviced Fiss weight sensing devices will work for many years.