FISS exports BÜHLER Carat 140, BÜHLER Evolution and more from Israel to Slovenia: A journey full of adventure
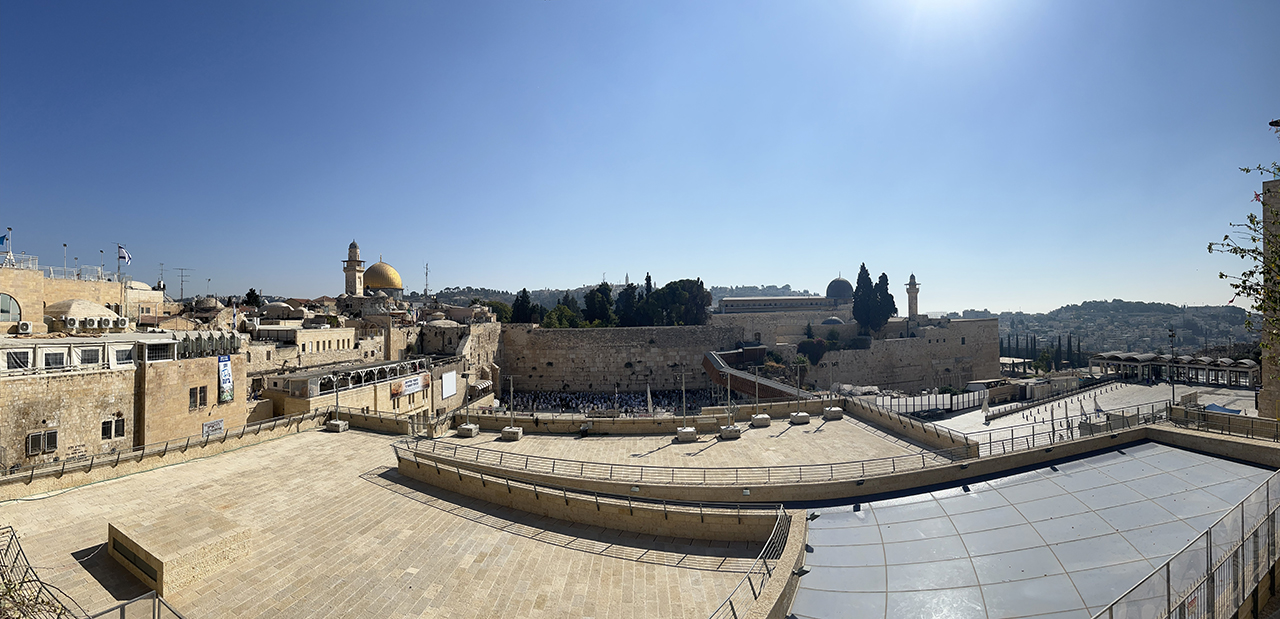
In 2022, FISS dismantled several BÜHLER die casting cells on behalf of a customer, packed them and shipped them to Slovenia as assemblies.
In 2022, FISS was commissioned by a company in Slovenia to find casting cells for the production of automotive parts on the international market for used machines for purchase. As an expert in used machinery, FISS not only organised the research and sale, but also the dismantling and transport of the machines. With a lot of expertise and care, they dismantled the machines, packed them and sent them on their way. An adventurous undertaking, but one that went well in the end. Among them were BÜHLER Carat tried and tested real-time controlled die casting machines with clamping forces of up to 14,000 kN and are particularly suitable for casting aluminium and magnesium parts in the automotive industry.
ADVICE AND NETWORK
In order to receive the best possible advice, the customer sought the support of the experienced experts at FISS. Thanks to the worldwide connections and close cooperation with sales partners from the die casting industry in almost all countries in the world, the suitable supplier of the used die casting machines in Israel was quickly located through extensive research. The customer was looking for casting cells for the production of aluminium housings for the automotive industry at its site in Slovenia and the extensive deal was quickly agreed as time was somewhat pressing.
PLANNING AND DISMANTLING
Now it was time to forge the planning for the demanding dismantling and relocation of the used machines. This is where the specialist knowledge of FISS came into play, whose 30 years of experience provided indispensable help. Together, the special challenges that could arise during dismantling and transport were scrutinised and practical solutions developed. The careful preparation and know-how of FISS ensured a successful implementation of the relocation.
The project was very extensive and included the dismantling and loading of: several BÜHLER Carat and Evolution die-casting cells with extensive automation equipment, StrikoWestofen aluminium melting furnace, Rösler linear flow continuous systems and Yxlon X-ray system and other foundry accessories.
The challenge with this project was to complete it within a very short time. There was not much lead time. The work was done in several shifts, even on Saturdays and Sundays. A team of 18 men was deployed, consisting of the client's employees and our dismantling team.
TRANSPORT AND ASSEMBLY
As a general contractor, FISS is the perfect contact for customers from the casting industry for the transport of complete casting plants. These transport tasks require a high level of expertise and customised planning to ensure that all steps of the project mesh smoothly. At FISS, customers can rely on decades of experience and sophisticated process management to bring every transport to a successful conclusion.
The documentation of the disassembly process was excellent. Each part was labelled and photographed and the client was kept informed throughout the process. One challenge of this project was that the machines had to be dismantled in Israel and most people there only speak Hebrew.
The transport included 18 loading units with 40-foot OTC, 13 loading units with 40-foot MAFI and a wooden crate with a Yxlon X-ray system, totalling about 550 tonnes. Despite the good preparation, adventurous challenges sometimes arise over which FISS has no control. The shipping company had to change the transport route at short notice and postpone the loading date. This led to an unplanned sea crossing of about 3 weeks.
The customer in Slovenia decided to carry out the assembly and commissioning of the machines themselves, but the FISS team was ready to provide any support. The set-up per casting cell took about 4 months.
Conclusion:
Overall, the project was a big task in terms of time and scope, but the professional planning and good teamwork enabled it to be completed successfully. The customer is very satisfied with the delivered die casting cells and ready for the production of automotive parts. FISS has been in contact with this customer for years and is looking forward to future cooperation.