Partial overhauling of Italpresse IP 750 SC cold chamber die casting machine
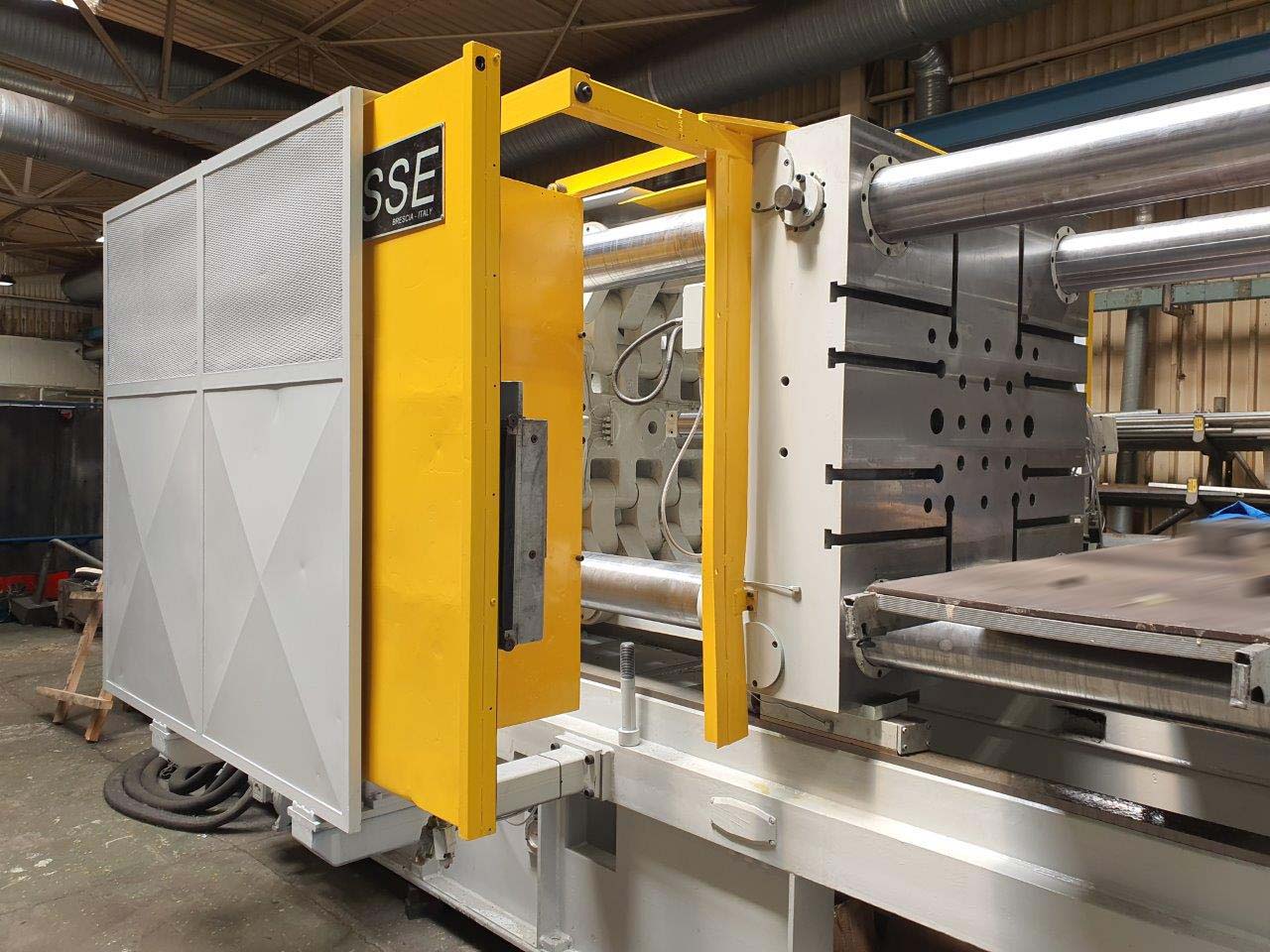
Year: 2002, incl. Italpresse VS-2 ALL. metal loader, for aluminium die casting
Scope of service:
1 General preparatory work
1.100 Clean, dismantle and visually inspect the machine. ✓1.110 Check and measure mechanical parts ✓
Clamping unit
2.100 Guide columns2.150 4 new guide columns ✓
2.160 4 new column nuts (front) ✓
2.200 Fixed clamping platen
2.210 Mill the fixed clamping plate flat ✓
2.230 Check or re‐machine mounting hole for guide column ✓
2.300 Movable clamping plate
2.310 Mill the movable clamping plate flat ✓
2.320 Rework T‐slots, if necessary ✓
2.330 Check or renew guide bushes ✓
2.340 Check bores for toggle system, replace defective guide bushes ✓
2.350 Check mounting surface for the sliding shoes and rework guide plates ✓
2.400 Toggle system
2.410 Check toggle system ✓
2.420 Re‐manufacture and install defective guide pins and guide bushes ✓
2.430 Check crosshead bores, replace defective guide bushes and guide pins ✓
2.450 Check or rework mounting hole for locking cylinder ✓
2.451 Check central lubrication, replace defective tubes and lubrication distributors. ✓
2.460 Check motorised central lubrication and check function ✓
2.500 Crosshead
2.510 Check bores for guide bushes, rework if necessary ✓
2.520 Replace and fit defective guide bolts and guide bushes. ✓
2.530 Check column nuts for central mould height adjustment, renew if necessary ✓
2.540 Check locking cylinder incl. piston, if necessary overhaul and reseal ✓
2.550 Check the mounting surface for the slide shoes, renew the guide plates. ✓
3 Hydraulic ejector
3.100 Replace defective guide pins and guide bushes ✓3.130 New hydraulic ejector seal ✓
4 Machine bed
4.100 Clean hydraulic tank ✓4.110 Check or rework the mounting surfaces for the guide rails ✓
5 Cylinders/seals
5.100 Dismantle clamping, ejector and press‐in cylinders as well as multiplier and check dimensions. ✓5.120 Replace seals and guide tapes ✓
5.130 Seal the closing, ejector and impression cylinders as well as the multiplier. ✓
6 Injection system
6.100 Dismantle and check the injection unit ✓6.110 Grind and hard‐chrome the multiplier and piston rod. ✓
6.131 Accept new piston accumulator and pressure vessel with test certificate ✓
7 Hydraulics
7.100 Check hydraulic pump with pump drive for wear ✓7.130 Check hydraulic pipe connections for leaks and cracks, replace if necessary ✓
9 Machine wiring
9.100 Check connection cable machine ‐ control cabinet, replace if necessary ✓10 Machine control
10.100 Check existing machine control with monitor, repair if necessary. ✓10.110 Check existing machine control, install new GEFRAN monitor with software
11 Interfaces
11.100 Check interfaces for metal dosing unit / dosing furnace ✓11.300 Check interfaces for spraying machine ✓
11.500 Check interfaces for robots ✓
12 Safety doors and safety covers
12.100 Check or repair motorised safety door on operator side ✓
12.110 Check closing part cover on the front and rear of the machine, repair if necessary. ✓
13 Painting
13.100 Prepare machine components for painting13.110 Paint machine, colour: grey RAL 7035 ✓
13.120 Paint protective doors and protective cover, colour: yellow RAL 1004 ✓
15 Dry run and final inspection
15.100 Trial run with function check ✓15.110 Final acceptance by the client ✓