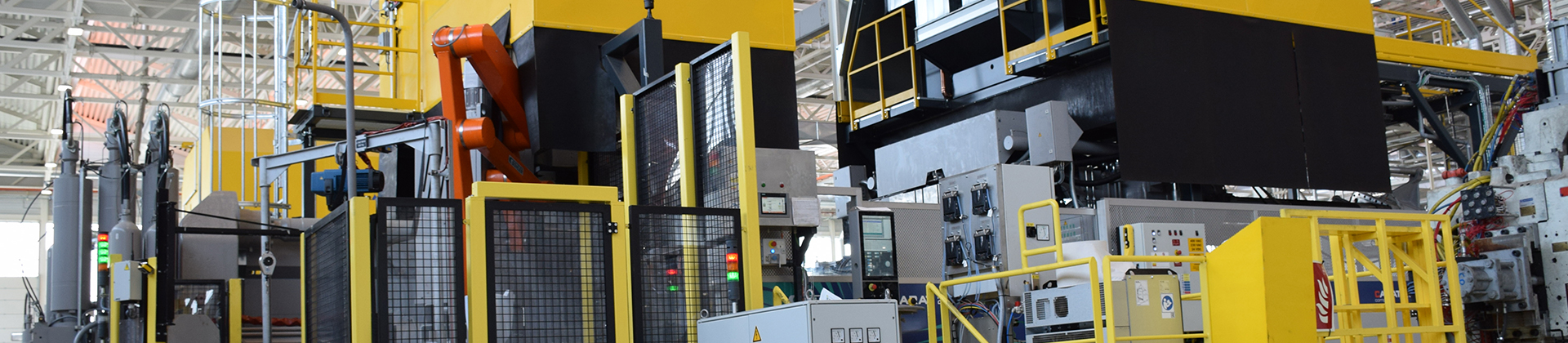
- Home
- Used Machines
- News
- Search Machines
- Your Offer
- Accessories
- Service
- Events
- About us
- Contact
Cold chamber die casting machines are preferred systems for processing light metals with high melting points to serial-casting-parts. They are very popular in the production of aluminium parts. A consistently high precision can be guaranteed even in large series with materials with thin wall thicknesses. Particularly complex structure and structural parts, like automotive engine blocks or door elements, are also producible with the cold-chamber-die-casting-process. Other metals that are processed using cold chamber die casting machines are magnesium and brass alloys.
Efficiency through automation and integration to casting cells
High quantities and short cycle times develop their greatest efficiency in automation as widely as possible. Belonging to the cold chamber die casting machines peripheral advices are therefore available in both manual and automated form. Thus, dosing furnaces, spraying machines, removal robots and trimming presses can be installed to automatically operating casting cells.
Distributed manufacturing-process
The special feature of the cold chamber manufacturing process is that the melting- and holding-process is separated from the manufacturing production process. In cold chamber die casting process, the liquid metal is supplied by a dosing furnace or a metal loader to the casting plant. The casting plant itself consists of pressing chamber and piston with piston rod which passes the liquid metal in the two-part, separable form. The so-called die casting mould is held together by the machine with a closing force of up to 45.000 kN. After the metal has solidified the mould halves are separated from each other. Due to the high weight and temperature of the cast parts, a foundry robot is usually used for the removal, which then precisely transports the casting part to the trimming press.
When filling the die casting mould, the air therein must be able to escape. Therefore so-called vent- and overflow-beans are incorporated into the mould. During the filling, those beans also get filled with liquid metal. In order to separate the beans from the product, trimming presses are used. After deburring, further processing steps may follow.
We are your experts around used die casting machines
No matter if you are interested in a casting cell with appropriate peripheral devices or looking for a cold chamber die casting machine without a corresponding automation. We, at Fiss, are experienced experts when it comes to buying and selling used die casting machines for the foundry industry.
The quality of the peripheral devices is crucial for cold chamber die casting machines to work as efficiently as possible for a long time. We offer you, in addition to a partial or complete revision of the die casting machine, a number of new and used peripheral devices for automation as well.
More than 30 years of experience and accordingly successful disassembly and re-assembly of used systems for foundry industry prove our expertise. In addition to highly qualified engineers and technicians, we offer you a comprehensive full-service, ranging from disassembly and overhaul of the machine, to the acquisition of logistics, installation and briefing at the new location.
Let us convince you of our individual services and rely on the experts at Fiss Machines!